Advertiser content
Clean energy? Stage V diesel fits the bill
Provided by
Cummins Inc., a global power leader, is a corporation of complementary business segments that design, manufacture, distribute and service a broad portfolio of power solutions. The company’s products range from diesel, natural gas, electric and hybrid powertrains. Cummins Performance Series engines for agricultural applications range from 37 to 503 kW (49 - 675 hp), offering the flexibility to match the right power solution for a wide range of farming applications and equipment including combine harvesters, sprayers, tractors and loaders, as well as specialised equipment
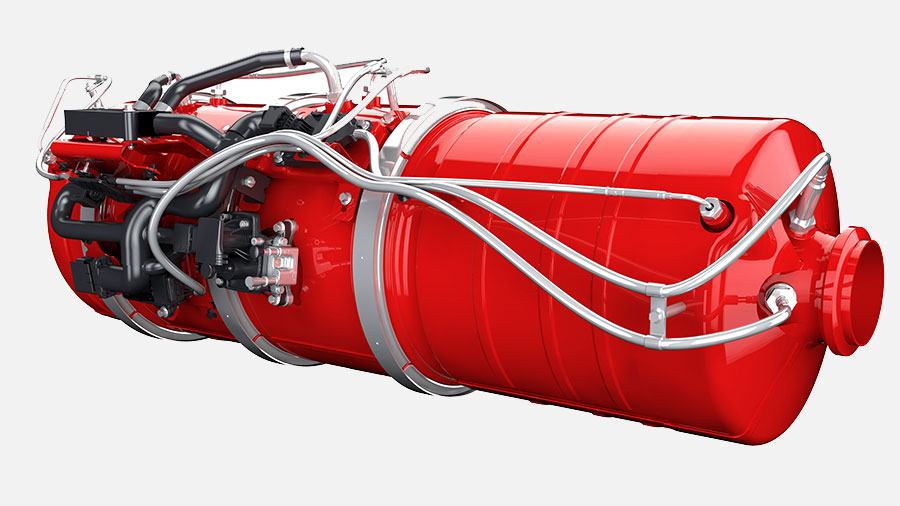
Whether it’s tractors, combine harvesters, sprayers or other self-propelled equipment, there is currently little substitute for diesel power.
But, against a backdrop of global climate change and new emissions legislation, Ann Schmelzer, general manager for agriculture at Cummins explains how engine aftertreatment technology works to make European diesel power the cleanest in the world.
What can often go unnoticed is the fact that the technology involved in diesel combustion has never been cleaner.
Emissions removal technology
EU Stage V legislation, which came into effect in January 2019 and January 2020, tightened oxides of nitrogen (NOx) emissions from off-road machinery as well as, for the first time, setting a strict limit on particulate matter emissions.
Stage V represents a 96% emissions reduction since legislation began in 1999.
Exhaust aftertreatment is technology used to remove emissions from a diesel engine ‘downstream’ of its combustion chamber and there are several options available to engine manufacturers.
Exhaust gas recirculation (EGR) and/or selective catalytic reduction (SCR) is used to remove NOx and a diesel oxidation catalyst (DOC) and/or a diesel particulate filter (DPF) removes particulate matter.
Acronyms aside, an internet search for “SCR vs. EGR’ will return more than two million results. Here’s a simple guide to the key technologies used to remove NOx to help you choose what’s best for your engines.
EGR
With Exhaust Gas Recirculation (EGR) a percentage (typically 25-35%) of the diesel engine’s exhaust gases are redirected back into the combustion cylinder to help reduce NOx emissions.
This happens as a result of a reduction in oxygen concentration, thereby leading to a lower temperature burn. As NOx is produced when nitrogen and oxygen mix in high temperatures, reducing the temperature reduces NOx production.
EGR can increase particulate matter, which is then removed by a diesel oxidation catalyst (DOC) and diesel particulate filter (DPF) – more on this in the particulate matter section.
EGR is considered to be an easy-to-use system and is fitted on Cummins’ Tier 4 Final engines for the North American market.
Selective catalytic reduction (SCR)
Selective catalytic reduction (SCR) is an exhaust aftertreatment technology that injects AdBlue into the hot stream of exhaust gases, where it breaks down into ammonia.
The ammonia is then used by the catalytic convertor to convert NOx into harmless nitrogen gas (N2) and water vapour (H2O).
Any trace amounts of left-over ammonia are broken down into nitrogen using a ‘slip’ catalyst.
Cummins Single Moduleâ„¢ aftertreatment
SCR is used as part of the innovative Single Module™ aftertreatment on Cummins’ Performance Series engines from 3.8 to 9 litres displacement.
Cummins Single Moduleâ„¢ aftertreatment combines SCR with particulate matter reducing technology and is up to 40% smaller and 20% lighter than its Stage IV predecessor.
SCR technology can achieve higher power delivery and better fuel economy due to increased combustion efficiency.
No recirculated air enters the engine, so the combustion temperature is optimised.
These benefits have been proven in Cummins’ Stage V 75 – 321 kW engines, which deliver, on average, 10% more power and 20% higher torque than at Stage IV, alongside higher reliability as a result of cleaner combustion.
For particulate matter, there are two main aftertreatment options – a diesel oxidation catalyst and a diesel particulate filter.
The two main aftertreatment types explained
A diesel oxidation catalyst (DOC)
A diesel oxidation catalyst (DOC) is a honeycomb-shaped filter with a catalytic coating.
The filter oxidises carbon monoxide, hydrocarbons and particulate matter from the exhaust stream turning them into water and CO2. DOCs are used in conjunction with DPFs, and modern systems support SCR function.
Diesel particulate filter (DPF)
The limit in particulate matter emissions at Stage V mandates the use of a diesel particulate filter (DPF), which features a semi-porous, usually ceramic, core which traps particulate matter as it passes through.
The particulate matter is then burned off through passive or active regeneration. Passive regeneration occurs when the exhaust temperature reaches a specific level, for example a combine harvester operating at rated speed and mid to high load during harvest.
This allows the clean burn-off of soot in the filter. Conversely, in active regeneration fuel is injected automatically when the DPF reaches a set limit to increase the temperature of the exhaust gases and burn off the soot.
Cummins’ Single Module™ aftertreatment system includes a DOC and DPF with advanced catalyst technologies for greater ash capacity.
Passive regeneration minimises the need for active regeneration and preventative cleaning. This helps to reduce both fuel used and provide longer maintenance intervals.
Engine performance benefits
But does aftertreatment technology reduce engine performance?
No. At Stage V, Cummins pushed the diesel engine onto the next rung of its revolutionary ladder, achieving near-zero emissions levels with Single Moduleâ„¢ aftertreatment while increasing average power and torque across the range.
It’s also not a case of which is best – EGR or SCR, it’s about choosing the right system for the application.
The diversity of agricultural equipment, as well as its international use, introduces factors like running costs, maintenance requirements, fuel consumption and engine commonality across regions.
It’s not always a one-size-fits-all scenario. What we do know is that with Stage V technology, Europe is delivering the world’s cleanest diesel power.