Top tips for upping the quality of farm workshop projects
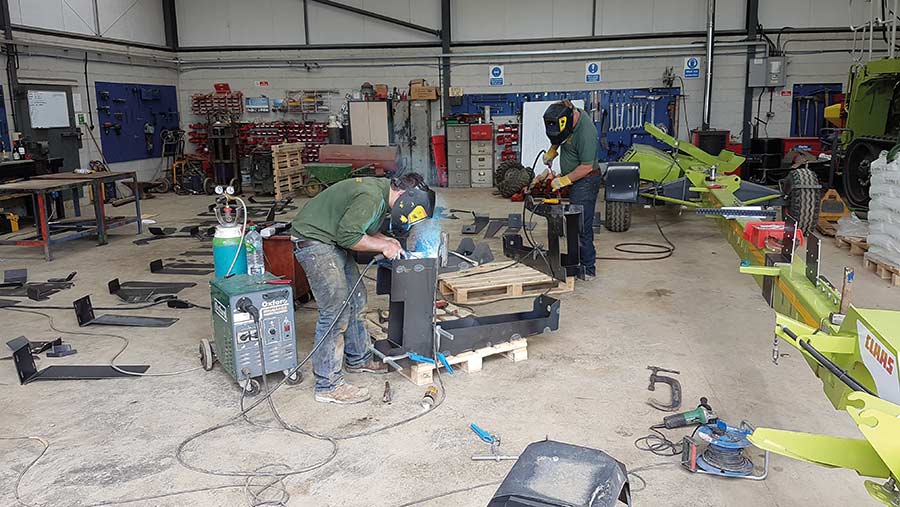
Every year, the Farm Inventions Competition unearths a horde of impressive workshop builds that provide ingenious answers to some of agriculture’s recurring conundrums.
Traditionally, farmers and contractors have sketched out designs for their project on a scrap of paper, before setting to work with the gas torch and welder, tweaking and modifying their creation as they go along.
But recent years have seen the introduction of some more sophisticated computer-aided design (CAD).
This, in turn, has given access to precision engineering such as laser and profile plasma cutting, press brake bending and high-tech 3D printing that can produce intricate bespoke parts.
The pioneers of this tend to be young graduates, putting their agricultural engineering degree skills to practical use.
However, there’s nothing to stop the older generation getting involved, with freelance help on hand to turn scribbles into digital designs.
This article looks at the range of services on offer, picks out a few individuals that have incorporated them into their projects and shows how others can get involved.
See also: Managing welding fumes on farms – all you need to know
Laser cutting
Affordable plasma cutters have made the process of carving up metal on farm far more accurate than the old gas axe or angle grinder.
But to get a truly professional finish with razor-sharp edges, it is worth considering laser cutting.
It might sound like an expensive luxury, but it offers pinpoint accuracy and makes assembly of projects far more straightforward.
Opting for this technique requires plenty of forward planning, rather than the age-old approach of making it up as you go along.
Those that have access to CAD software, and have the skills to use it, can simply email a DXF file of their project to the laser-cutting firm.
For people who don’t, it is possible to sketch out the idea on paper and get someone else to draw it up for you.
Some laser-cutting firms will do this for an additional cost, but there’s also the option of using freelance CAD designers (see “Getting to grips with CAD” below).
Getting to grips with CAD
Computer-aided design (CAD) software is the key for outsourcing jobs such as laser cutting and 3D printing, but it can seem bewilderingly complex for the uninitiated.
Solidworks is one the most popular platforms for professional users and it comes with a host of add-on options, including the ability to carry out finite element analysis to test the strength of a design.
It is prohibitively expensive for the casual user, but there are some free online tools for those that want to have a go at sketching out simpler parts.
Examples include Sketchup, NanoCAD and Creo Elements, all of which offer a free, basic version with the option of adding paid features.
A simper alternative is to draft in the help of a friend with CAD experience or enlist the services of a freelance designer.
These can be found with a quick internet search, and some companies will also offer these services in-house.
Most of these will be generalists, but there are some that work predominantly in agriculture (see “Case study: Jonny Leech”, below).
Once appointed, a freelance designer will be able to take some simple hand sketches and transform them into the relevant computer files.
Rates start at about £25/hour, but some will charge on a project basis.
It shouldn’t be too expensive to have accurate hand designs redrawn, but prices will go up as the amount of creative work increases.
There are plenty of laser-cutting firms out there, and many will provide instant quotes once they’ve seen the design, or it has been uploaded to their website.
This makes it relatively quick to hunt around for the best prices and check lead times.
Costs savings can be made by producing multiples of the same part, which is something designers will consider when putting a project together.
Many laser-cutting firms will also have a press brake on site, making it possible to have profiles cut and bent to shape.
This opens the options, particularly for assembly techniques such as tab-and-slot, which allows adjoining pieces of metal to lock together.
As well as making the construction stronger, this speeds up the build time.
Profile plasma cutting is a cheaper alternative to laser. It is also computer controlled for improved accuracy, but the metal is sliced by a plasma tip, which fires out compressed air and inert gasses.
Results are similar, particularly when working with thick plate, but there’s more chance of thinner metals distorting, and it can’t cope with such intricate designs.
Case study: Jonny Leech
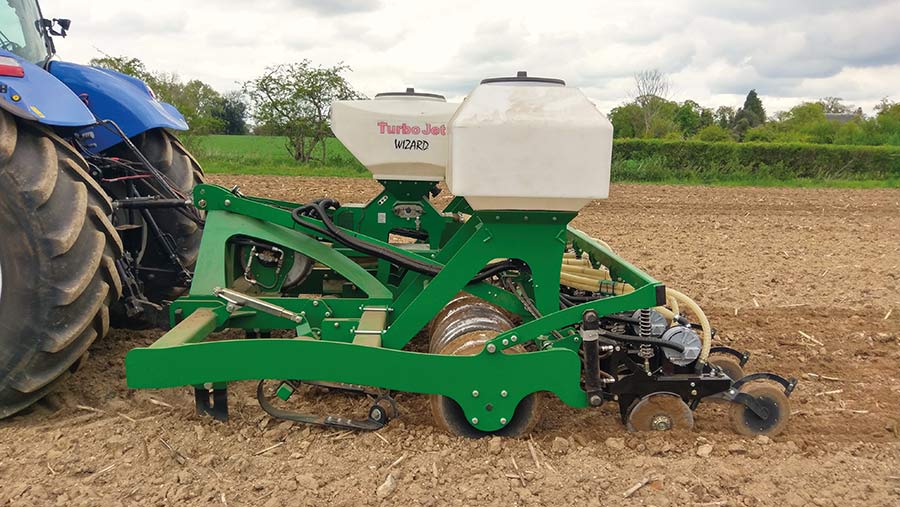
© Jonny Leach
When Norfolk farmer and designer Jonny Leech set about building a precision maize planter, he decided to go the whole hog and make his own singulation units.
To do this he purchased a £175 3D printer in kit form and began churning out custom plastic components that were a fraction of the cost of off-the-shelf alternatives.
Design work was carried out in Solidworks, and he produced about 15 prototypes before settling on a design that gave him 99% singulation accuracy at 12kph.
At the time, units sold by the main manufacturers were about £500 each, but the cost of printing parts for all his units were just £10 apiece.
Before buying his own printer, he got a few parts produced by a 3D printing firm. However, it was expensive at the time, particularly as he was at the prototyping stage.
Purchasing his own printer gave him much more flexibility to play around and had the benefit of allowing him to produce his own low-cost replacement parts.
The problem with having an entry-level printer is that it only works with a limited range of plastics, which aren’t that durable. As a result, Mr Leech is looking to upgrade to a more sophisticated model.
Construction of the drill’s chassis was also outsourced to a local fabricator and the metal for the frame was profile plasma cut to improve accuracy.
Mr Leech honed his CAD skills when working as a design and test engineer for Great Plains.
He now runs his own freelance business, JL Design, which specialises in creating bespoke agricultural machinery.
He charges £25/hour and can either convert hand drawings into computer files or produce custom designs from scratch.
He also works with a local fabricator so that those lacking workshop skills or time can have their project built for them.
3D printing
The world of 3D printing can seem wildly complex and inaccessible, but even those without the knowledge and equipment to do it themselves can tap into the benefits.
These include sourcing one-off parts for a project, reproducing obsolete components or even finding a cheaper alternative to small-but-pricey items sold by manufacturers.
The process is largely the same as a regular printer, but rather than putting ink on a page, they build up layers of plastics or metals to form three-dimensional parts.
Those with CAD software can draw the item on a computer and the printer will automatically bring it to life.
Entry-level printers can be purchased for a couple of hundred pounds, but the prices start to rise when you want to work with a wider range of materials or print larger items.
For those that would rather not go through the rigmarole of buying and running their own printer, there are plenty of firms that will do the job for you.
One example is 3D Alchemy in Shropshire, which specialises in bespoke 3D printing services. It works with a huge range of materials from ABS plastic and rubbers to aluminium, titanium and carbon.
Prices for simple plastic items can be in the tens of pounds, while one-off aluminium parts start at about £200. Ordering multiple parts can bring these prices down though.
Like running your own machine, 3D printing firms will need a CAD drawing to print from (see “Getting to grips with CAD”, above).
Case study: Hywel Phillips
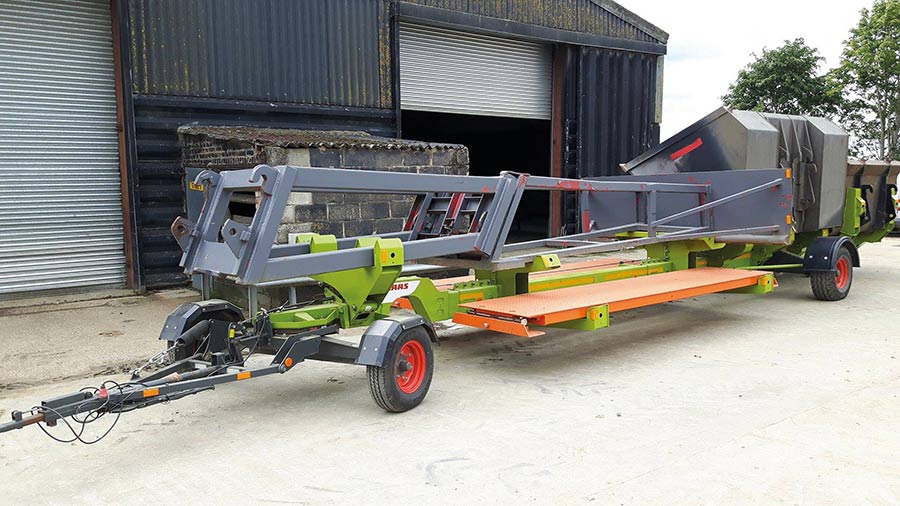
© Hywel Phillips
Harper Adams engineering graduate Hywel Phillips used laser cutting when modifying a spare Claas header trailer so that it could carry a grain pusher, large bucket and weigh cells.
The project was for an arable farm in Essex where he used to work, and he carried out all the design work in Solidworks CAD software.
Once he was satisfied with the plans, he sent his drawings to Accurate Laser Cutting in Birmingham, which cut out all the profiles and delivered them to the farm on a couple of pallets.
In total, there were 162 pieces of 6mm and 8mm steel plate cut into a series of shapes, roughly half of which also had some bends produced on the firm’s press brake.
The total bill at the time (2017) was just over £1,500.
The reason for the bending was that Mr Phillips used a tab-and-slot construction method. This added strength and made it quick for the farm to construct, without any further input from him.
By using Solidworks, he was also able to carry out stress testing and make sure that he had included just the right amount of metal.
Five years later, the trailer is still going strong, and it hasn’t required any modifications.
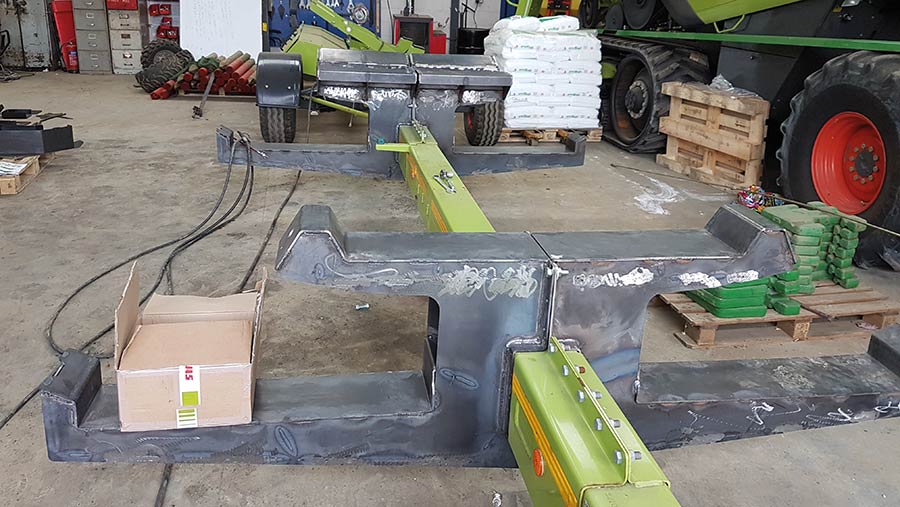
© Hywel Phillips
“They were a bit dubious about the fact I used no-section steel, but once all the plate was welded together, it was far stronger and stiffer,” he says.
Mr Phillips reckons this approach to farm workshop builds could work for many farms. “So many farmers are good at welding and fabrication, but lack the computer design skills,” he says.
By getting a designer to do that work for them, they should be able to build their project faster, waste less metal and not have to make modifications as they go along.
Bending steel
Manipulating large chunks of steel in a farm workshop can be a challenging process, so it’s worth looking into the services of professional bending firms.
There are plenty of options for lighter metals – many laser-cutting firms have press brakes – but as the metal gets thicker and longer, the job becomes more specialist.
Barnshaws is one of the largest operators in the UK and has depots in the West Midlands, Manchester and Hamilton near Glasgow.
It can fold sheet metals up to 80mm thick, has rollers for forming pipes, and can bend heavy section steel in lengths of up to 35m.
West Midlands firm Angle Ring offers a similar range of services.
Case study: Andrew Burt
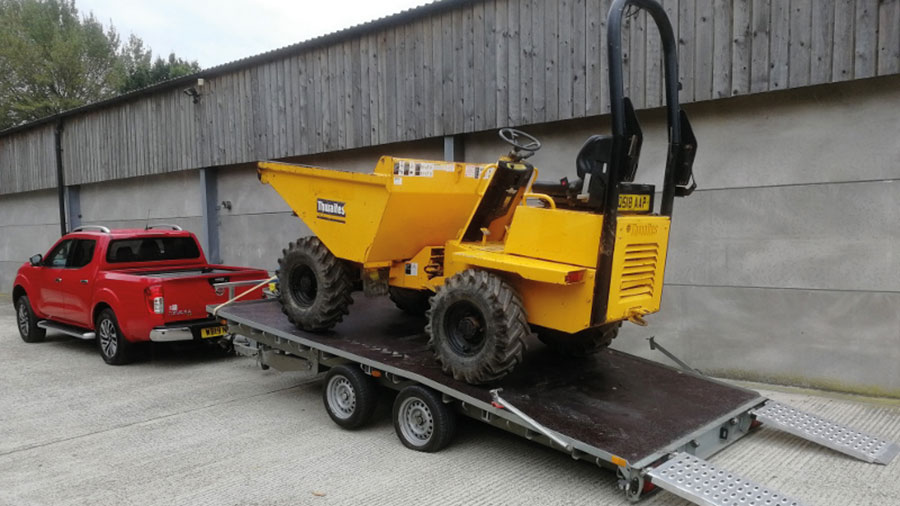
© Andrew Burt
Andrew Burt has built a range of high-quality lifting, winching and towing gear for his recovery and engineering business AB Machinery.
For each of these, he sketched out the designs by hand and carried out all the fabrication work himself.
However, in order to get the quality of finish he wants, he has outsourced some of the jobs to specialist firms.
When it came to building a land-anchor winch, for lowering a winder turbine and recovering stuck vehicles, he decided to have some of the more complex components cut with a profile plasma cutter.
Without CAD software, or the skills to use it, he enlisted the help of a friend who works in Formula One.
He took Mr Burt’s scale drawings and converted them to digital CAD files before sending them to the cutting firm.
The base plate for the winch is made from a piece of 1in thick base plate and he wanted the edges bent up so that it wouldn’t dig into the ground.
This would have been impossible in his workshop, so he sent the plate to West Midlands firm Barnshaws, which bent it on a heavy-duty press brake.
Another of his projects was to build a high-spec tilt-bed trailer for moving machinery.
This was completed four years ago, and he decided to have the chassis hot-dip galvanised to protect it from the elements.
He sent it to Joseph Ash and the price was about £180.
Galvanising
Galvanising isn’t as high tech as the rest of the processes mentioned, but it remains a valuable service for helping workshop projects stand the test of time.
Coating steel in molten zinc causes tough alloys to form that protect the metal from corrosion and give it a possible lifespan of up to 170 years.
Because products are submerged in a vat of molten zinc, both outside and inside surfaces are coated, giving maximum protection. For this reason, a degree of preparation needs to be made before sending items to the galvanisers.
For example, if coating an item with a closed box-section steel in its construction, holes will need to be made so that the molten zinc can enter and excess material can drain away.
Galvanisers will send out a detailed guide showing where these need to be placed, but the basic principle is that openings are made at either end of each sealed section, diagonally opposite one another.
Drilling is one option, but “V” and “U” notches can be used as an alternative, as well as griding off the corners of sealed sections.
The larger the holes, the faster the dipping process is and the better the finish will be, so it’s best not to be too mean when making them.
It’s also important to make sure the metal is rust-, paint- and grease-free, as any contaminants will interfere with the process.
Galvanisers will inspect all items when they arrive to make sure they are suitable, and any problems can be rectified before they’re put through the process, but it’s best to sort this before sending.
The galvanising process is relatively straightforward, beginning by degreasing the steel and treating it with hydrochloric acid to remove any final traces of rust or mill scale.
It’s then lowered into a zinc, ammonium chloride flux solution to remove the last traces of iron oxide, before it’s dipped in the molten zinc galvanising solution, which is heated to 450C.
Items stay in the liquid for about five minutes – slightly longer for larger pieces – and when they’re removed, any excess zinc is wiped away before leaving them to dry.
Prices are based on the weight of the completed item, and these vary according to the type of product being dipped. As a guide, the current price to galvanise a Land Rover Defender chassis is about £400.
Those that want the protection of galvanising with a painted surface can opt for a powder coat to be applied over the zinc.
Many galvanisers now offer this as a service, as it’s best applied soon after dipping. It works by spraying powdered paint onto the surface, which is then baked to give it a smooth, tough finish.
Case study: Jim Tarry
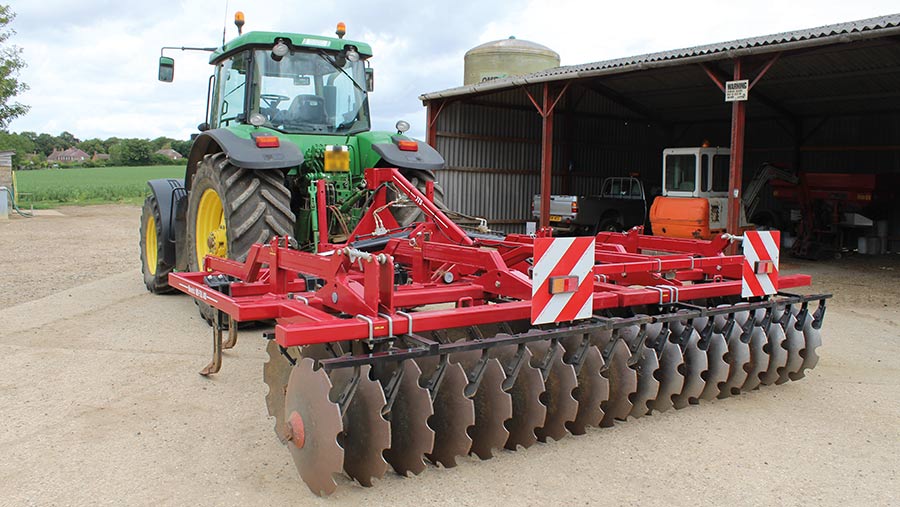
© Jim Tarry
Jim Tarry runs his own engineering business in Suffolk called JTS machinery, which specialises in building, modifying and repairing agricultural machinery.
One of his bespoke machines is a low-draft primary cultivator called the Maverick, which works the soil 125mm-250mm (5-8in) deep, leaving the soil open, rather than pressed down by a packer roller.
Much of the steel in its construction is laser cut to improve the accuracy and make construction simpler. Mr Tarry doesn’t use CAD software, but he produced a series of detailed hand drawings of the parts.
These were sent to steel stockholder and processor AJN Steelstock, which redrew them in the computer before they were sent to the cutting machine.
The parts then arrived on a pallet ready for him to fabricate into the machine. “It’s an added expense, but you just can’t get the same level of accuracy when cutting out steel by hand in the workshop,” he says.